So, you’ve found yourself in a situation where you need to work with chemicals. It could be for a school project, a job, or maybe just because you have a curious mind. Regardless of the reason, one thing is for sure – you want to stay safe while handling these potentially hazardous substances. That’s why we’ve put together this article to provide you with some practical and effective safety tips for working with chemicals. From proper storage and handling techniques to personal protective equipment, we’ve got you covered. So, let’s dive right in and ensure you have a safe and successful chemical experience!
1. Personal Protective Equipment (PPE)
1.1 Understanding PPE Requirements
When working with chemicals, it is crucial to prioritize your safety by wearing the appropriate personal protective equipment (PPE). PPE acts as a physical barrier between you and potential hazards, reducing the risk of exposure to chemicals. Understanding the PPE requirements specific to your workplace is essential for ensuring your safety.
PPE requirements can vary depending on the chemicals you work with and the tasks you perform. Some common types of PPE include safety goggles or glasses, gloves, lab coats or aprons, and respiratory protection such as masks or respirators. These types of equipment are designed to protect specific areas of your body that may come into contact with chemicals.
To determine the PPE requirements for your workplace, consult your company’s safety guidelines and relevant industry standards. These resources will provide detailed information on the specific types of PPE you should wear, when to wear them, and how to properly use and maintain them.
1.2 Appropriate Selection of PPE
Selecting the appropriate PPE is crucial to ensure maximum protection against chemical hazards. Different chemicals can have varying effects on the body, so it’s essential to choose PPE that is specifically designed to guard against the potential risks associated with the chemicals you handle.
When selecting PPE, consider the following factors:
- Chemical Compatibility: Ensure that the PPE you choose is resistant to the chemicals you work with. Some chemicals can degrade or permeate through certain types of PPE, rendering them ineffective.
- Comfort and Fit: PPE should fit properly to provide optimal protection. Ill-fitting equipment can be uncomfortable and may not adequately shield you from chemical exposure. Take your measurements and consult sizing charts to ensure a proper fit.
- Accessibility: PPE should be readily accessible to all employees who require them. Consider the ease of use and practicality of the equipment when selecting PPE for your workplace.
Remember, PPE is your last line of defense against hazardous chemicals, so it is crucial to select the right equipment for the job.
1.3 Proper Use and Maintenance of PPE
Equally important to selecting the appropriate PPE is using and maintaining it properly. PPE can only protect you if it is used correctly and kept in good condition.
Here are some essential tips for using and maintaining PPE:
- Follow Proper Donning and Doffing Procedures: Learn and follow the correct procedures for putting on (donning) and removing (doffing) your PPE. Improper handling can lead to contamination or injuries.
- Regular Inspection: Inspect your PPE before each use for any signs of damage or wear. Look for tears, holes, or other defects that may compromise its effectiveness. If any damage is found, replace the equipment immediately.
- Cleaning and Decontamination: Clean and decontaminate your PPE after each use according to the manufacturer’s instructions. This helps remove any residual chemicals and ensures the equipment is ready for the next use.
- Proper Storage: Store your PPE in a clean and dry area away from direct sunlight and extreme temperatures. Proper storage helps prolong the lifespan of your equipment and maintains its effectiveness.
By following these guidelines, you can ensure that your PPE functions as intended and provides you with the necessary protection against chemical hazards.
2. Chemical Handling and Storage
2.1 Proper Labeling and Identification
Proper labeling and identification of chemicals are crucial for maintaining a safe working environment. Labels provide important information about the contents of containers, including potential hazards and required precautions. It is essential to understand and follow the labeling system used in your workplace to avoid accidents or exposure to harmful substances.
When handling chemicals, make sure to:
- Read Labels Carefully: Before using any chemical, thoroughly read and understand the information provided on the label. Pay attention to hazard symbols, precautionary statements, and first aid instructions.
- Do Not Remove or Deface Labels: Labels should be intact and legible at all times. Removing or defacing labels can lead to confusion and increase the risk of accidents.
- Replace Damaged or Illegible Labels: If a label becomes damaged or illegible, request a replacement immediately. Unclear labeling can result in incorrect handling or storage of chemicals.
By adhering to proper labeling and identification practices, you can ensure the safe handling of chemicals and minimize the risk of accidents or exposure to hazardous substances.
2.2 Compatibility of Chemicals
Chemicals can interact with one another, leading to potentially dangerous reactions. It is crucial to understand the compatibility of chemicals to prevent accidental mixing or storage of incompatible substances.
Consider the following guidelines for handling chemicals safely:
- Segregate Incompatible Chemicals: Store chemicals according to their compatibility groups. Segregate incompatible substances to reduce the risk of chemical reactions. Consult the Safety Data Sheets (SDS) or other resources for guidance on chemical compatibility.
- Avoid Mixing Unknown Chemicals: If you are unsure of the contents or reactivity of a chemical, avoid mixing it with other substances or disposing of it improperly. Seek guidance from a qualified professional or contact the manufacturer for clarification.
- Understand Chemical Incompatibilities: Some chemicals have well-known incompatibilities. For example, acids and bases can react violently when mixed. Educate yourself on the potential hazards and reactions associated with the chemicals you handle.
By following these practices, you can prevent accidental mixing of incompatible chemicals and reduce the risk of hazardous reactions.
2.3 Safe Storage Practices
Proper storage of chemicals is essential to minimize the risk of accidents, spills, and exposure. Implementing safe storage practices will help maintain a well-organized workplace and ensure the integrity of chemicals.
Consider the following guidelines for safe chemical storage:
- Dedicated Storage Areas: Designate specific storage areas for different types of chemicals based on their hazards and compatibility. Separate flammable, corrosive, toxic, and reactive substances to prevent unintended chemical reactions.
- Secure Containers: Store chemicals in securely closed containers to prevent leaks, spills, or accidental exposure to the contents. Containers should be made of appropriate materials that are compatible with the chemical being stored.
- Proper Ventilation: Ensure that storage areas are well-ventilated to reduce the build-up of potentially hazardous vapors or gases. Good ventilation helps maintain air quality and minimizes the risk of chemical exposure.
- Temperature Control: Some chemicals may have specific temperature requirements for storage. Ensure that you are storing chemicals within the recommended temperature range to maintain their stability and prevent degradation.
By implementing these storage practices, you can create a safer work environment and reduce the likelihood of accidents or chemical hazards.
2.4 Transporting Chemicals Safely
Transporting chemicals from one location to another can pose additional risks if not done safely. Whether you are moving containers within your workplace or transporting them off-site, it is crucial to follow proper handling and transport procedures.
Consider the following safety tips when transporting chemicals:
- Use Properly Sealed and Labeled Containers: Ensure that all containers are tightly sealed and properly labeled before transporting them. This prevents leaks and minimizes the risk of accidental exposure.
- Secure Containers During Transport: When moving containers, ensure that they are stable and cannot tip over or fall. Use appropriate handling equipment, such as trolleys or carts, to safely transport heavy or bulky items.
- Separate Incompatible Chemicals: If transporting multiple chemicals, separate incompatible substances to prevent accidental mixing or reactions during transport.
- Follow Regulatory Requirements: Familiarize yourself with local, state, and federal regulations regarding the transport of hazardous materials. Compliance with these regulations is crucial to ensure the safety of yourself and others.
By following these transport guidelines, you can reduce the risk of accidents, spills, or exposure during the movement of chemicals.
3. Risk Assessment and Hazard Communication
3.1 Identifying Chemical Hazards
To promote a safe working environment, it is essential to identify and understand the hazards associated with the chemicals you handle. Chemical hazards can manifest in various ways, such as toxicity, flammability, or reactivity. Conducting thorough hazard assessments allows you to implement appropriate control measures and reduce the risk of accidents or exposure.
Consider the following steps when identifying chemical hazards:
- Consult Safety Data Sheets (SDS): SDSs provide detailed information on the hazards and properties of chemicals. Review the SDS for each chemical you work with to identify potential health, fire, or environmental hazards.
- Review Workplace Processes: Assess how chemicals are used, handled, and stored within your workplace. Identify any potential sources of exposure or areas where accidents could occur.
- Involve Employees: Consult with employees who regularly work with chemicals. They may have valuable insights or identify hazards that may not be immediately apparent.
By conducting thorough hazard assessments, you can proactively identify and address potential risks associated with the chemicals you work with.
3.2 Performing Risk Assessments
Once chemical hazards have been identified, it is crucial to assess the level of risk associated with each hazard. Risk assessments help prioritize control measures and determine the appropriate safety protocols to implement.
Consider the following steps when performing risk assessments:
- Evaluate Exposure Routes: Identify the ways in which employees may come into contact with hazardous chemicals, such as inhalation, skin contact, or ingestion. Assess the likelihood and severity of potential exposure.
- Determine Risk Levels: Assign a risk level to each identified hazard, considering both the likelihood and severity of potential consequences. This helps prioritize control measures for higher-risk hazards.
- Develop Control Measures: Determine the control measures necessary to minimize or eliminate the identified risks. These may include engineering controls, administrative controls, or the use of PPE.
- Review and Update Assessments: Regularly review and update risk assessments as new chemicals or processes are introduced. Changes in the workplace should trigger a reassessment of hazards and risks.
By conducting thorough risk assessments, you can effectively mitigate potential hazards and create a safer working environment for everyone.
3.3 Understanding Safety Data Sheets (SDS)
Safety Data Sheets (SDS) are vital sources of information that provide detailed guidance on the safe handling, storage, and disposal of chemicals. Familiarizing yourself with SDSs is essential for understanding the hazards associated with chemicals and implementing appropriate safety measures.
Follow these guidelines for understanding and utilizing SDSs effectively:
- Accessing SDSs: Ensure that SDSs are readily accessible to all employees who work with or are potentially exposed to chemicals. They should be easily retrievable, whether in physical or electronic format.
- Reading and Understanding SDSs: Review SDSs for any chemicals you work with to gain a thorough understanding of their hazards, appropriate safety precautions, and recommended control measures. Pay attention to sections such as hazard identification, first aid measures, and handling and storage guidelines.
- Implementing SDS Recommendations: Use the information provided in SDSs to guide your safe handling, storage, and disposal practices. SDSs offer specific instructions to ensure the proper management of chemicals.
By utilizing SDSs effectively, you can ensure that chemicals are handled safely, and the associated hazards are minimized.
4. Emergency Preparedness
4.1 Creating an Emergency Response Plan
Preparing for emergencies is essential to minimize the impact of accidents or incidents involving chemicals. Having a well-defined emergency response plan in place ensures that everyone knows what to do in the event of a chemical spill, fire, or exposure.
Consider the following when creating an emergency response plan:
- Establish Emergency Procedures: Develop clear and concise procedures for various emergency scenarios. These should include steps for evacuations, contacting emergency services, and providing immediate medical assistance.
- Training and Communication: Provide comprehensive training to all employees on the emergency response plan. Regularly conduct drills and exercises to reinforce the procedures and ensure everyone is familiar with their roles.
- Locate Emergency Equipment: Identify the location of emergency equipment, such as fire extinguishers, safety showers, eyewash stations, and spill control kits. Ensure that they are easily accessible and employees know how to use them correctly.
- Coordinate with Local Authorities: Establish a strong working relationship with local emergency response agencies. Share your emergency response plan with them and seek their input or guidance, if necessary.
By creating an effective emergency response plan, you can minimize the potential harm caused by accidents or incidents involving chemicals and protect the well-being of your employees.
4.2 First Aid and Emergency Equipment
In the event of a chemical incident, immediate and appropriate first aid measures can significantly reduce the severity of injuries or illnesses. Having essential first aid equipment readily available is crucial for providing timely assistance to those in need.
Consider the following when addressing first aid and emergency equipment:
- First Aid Training: Ensure that designated employees receive proper first aid training, including CPR and the handling of chemical exposure incidents. These individuals should be knowledgeable and capable of providing immediate medical attention.
- First Aid Kits: Stock first aid kits with supplies that are appropriate for handling chemical-related injuries. These may include disinfectants, bandages, burn dressings, and eye wash solutions. Regularly check and replenish the supplies to keep the kits up to date.
- Safety Showers and Eyewash Stations: Install safety showers and eyewash stations in areas where chemicals are used or stored. Ensure that these emergency fixtures are functioning correctly, regularly inspected, and free from any obstructions.
By ensuring that first aid measures and equipment are readily available, you can effectively respond to chemical incidents and provide immediate assistance to those in need.
4.3 Spill Control and Containment
Chemical spills can occur, even with the utmost care and precaution. Prompt and effective spill control measures are essential to contain and manage spills to prevent further damage or harm.
Follow these guidelines for spill control and containment:
- Establish Spill Response Procedures: Develop well-defined procedures for responding to chemical spills. These should include steps for immediate notification, evacuations if necessary, and appropriate containment and cleanup measures.
- Spill Kits and Absorbents: Ensure that spill kits are easily accessible throughout your workplace. These kits should contain appropriate absorbents, neutralizers, and personal protective equipment (PPE) necessary for safe containment and cleanup.
- Proper Cleanup and Disposal: Train employees on proper cleanup procedures and disposal of spill-related materials. Promote responsible waste management to prevent environmental contamination or health hazards.
- Document Spills and Incidents: Keep a record of all spills and incidents, regardless of their severity. This documentation helps identify trends, implement corrective actions, and improve spill prevention measures.
By establishing spill control procedures and providing the necessary resources, you can effectively respond to chemical spills and mitigate their potential impact.
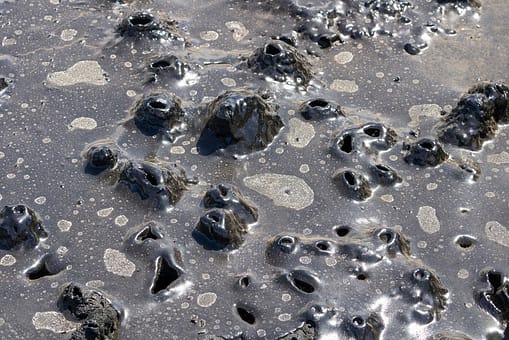
5. Ventilation and Engineering Controls
5.1 Importance of Adequate Ventilation
Proper ventilation is crucial to maintaining a safe and healthy working environment when working with chemicals. Ventilation systems help control airborne contaminants, reducing the risk of inhalation or exposure.
Consider the following reasons why adequate ventilation is essential:
- Dilution of Airborne Contaminants: Ventilation systems supply fresh air, diluting and dispersing airborne contaminants, including vapors and gases emitted by chemicals. This reduces their concentration and potential for exposure.
- Removal of Hazardous Vapors: Some chemicals emit hazardous vapors that can build up in confined or poorly ventilated areas. Adequate ventilation ensures the removal of such vapors from the work environment.
- Temperature and Humidity Control: Proper ventilation can help regulate temperature and humidity levels, creating a comfortable and productive workspace.
- Prevention of Combustible Atmospheres: In areas where flammable chemicals are present, ventilation helps prevent the accumulation of flammable vapors, reducing the risk of fire or explosions.
5.2 Types of Ventilation Systems
Different types of ventilation systems are available, and the selection depends on the nature of the workplace and the chemicals being used. The two primary types of ventilation systems are general ventilation and local exhaust ventilation.
- General Ventilation: This system provides fresh air throughout the entire workplace. It typically involves the use of fans and exhaust systems to circulate and replace air, ensuring a continuous supply of clean air.
- Local Exhaust Ventilation: This system captures and removes contaminants at their source, such as fume hoods or extraction arms located near chemical workstations. Local exhaust ventilation is particularly effective when working with highly toxic or volatile substances.
When designing or implementing ventilation systems, consult with professionals experienced in the field to ensure the most appropriate system for your specific needs.
5.3 Maintenance and Inspection of Controls
Proper maintenance and regular inspection of ventilation systems are necessary to ensure their effectiveness. Malfunctioning or poorly maintained systems can compromise air quality and potentially expose workers to hazardous chemicals.
Consider the following practices for maintaining and inspecting ventilation controls:
- Schedule Regular Inspections: Establish a routine inspection schedule to assess the condition and performance of ventilation systems. Engage qualified technicians or engineers to conduct these inspections.
- Clean and Replace Filters: Filters in ventilation systems can become clogged with dust, debris, or chemicals over time. Regularly clean or replace filters to maintain optimal airflow and filtration efficiency.
- Verify Airflow: Ensure that ventilation systems are providing the necessary airflow to effectively control airborne contaminants. Use instruments such as an anemometer or smoke tube to verify proper airflow.
- Monitor Carbon Monoxide Levels: If your workplace uses fuel-burning equipment, such as forklifts or furnaces, regularly monitor carbon monoxide levels to ensure the ventilation system is effectively removing this deadly gas.
By prioritizing maintenance and inspections, you can maintain a healthy working environment and ensure that ventilation systems are functioning properly.
6. Safe Work Practices
6.1 Training and Education
Proper training and education are crucial in promoting safe work practices when handling chemicals. Employees must have the knowledge and skills necessary to work safely and respond appropriately to potential hazards.
Consider the following guidelines for training and educating employees:
- Initial Training: Provide comprehensive training to all employees who work with or may be exposed to chemicals. This training should cover the identification of hazards, proper use of PPE, safe handling techniques, and emergency response procedures.
- Regular Refresher Training: Conduct periodic refresher training sessions to reinforce safe work practices and update employees on any changes in protocols, regulations, or chemicals being used.
- Written Procedures and Guidelines: Develop written procedures and guidelines that outline safe work practices. These documents should be easily accessible to all employees and serve as a reference for safe chemical handling.
- Encourage Questions and Communication: Encourage employees to ask questions or seek clarification regarding safe work practices. Foster open communication to ensure employees fully understand the potential risks and associated safety protocols.
By investing in proper training and education, you can empower your employees to make informed decisions and contribute to a safer work environment.
6.2 Minimizing Exposure
Minimizing exposure to chemicals is essential in reducing the risk of adverse health effects. By implementing effective control measures and safe work practices, you can significantly reduce the potential for exposure.
Consider the following strategies to minimize exposure:
- Substitute Hazardous Chemicals: Whenever possible, substitute hazardous chemicals with less harmful alternatives. Choose chemicals with lower toxicity, volatility, or reactivity to minimize potential hazards.
- Implement Engineering Controls: Utilize engineering controls, such as ventilation systems or automated processes, to minimize direct contact with chemicals and control their release into the work environment.
- Use Containers with Secondary Containment: Store chemicals in containers with secondary containment systems, such as trays or secondary containers, to prevent leaks or spills.
- Adopt Enclosed Systems: Enclosed systems, such as closed transfer systems or automated mixing processes, minimize the risk of exposure by reducing direct contact with chemicals.
By adopting these strategies, you can effectively minimize the potential for exposure and promote a safer working environment.
6.3 Proper Handling Techniques
Proper handling techniques are crucial in preventing accidents, spills, and exposure to hazardous chemicals. Following established protocols and safe work practices when working with chemicals is essential for maintaining a safe work environment.
Consider the following guidelines for proper handling techniques:
- Read Instructions and Labels: Thoroughly read and understand the instructions and labels provided by the manufacturer for each chemical you work with. Follow the recommended handling procedures and precautions.
- Use Appropriate Tools and Equipment: Use the correct tools and equipment for handling chemicals, such as properly sized containers, suitable dispensing equipment, and suitable ventilation systems.
- Avoid Unnecessary Exposures: Minimize the time spent in direct contact with chemicals. Avoid unnecessary exposure by handling chemicals in a well-ventilated area, using appropriate PPE, and reducing the reliance on manual handling.
- Practice Safe Pouring and Transfer: When pouring or transferring chemicals, use proper techniques to prevent spills or splashes. Use funnels, pouring spouts, or automated systems to reduce the risk of accidental contact.
By adhering to proper handling techniques, you can minimize the risk of accidents, spills, and exposure to hazardous chemicals.
6.4 Good Hygiene Practices
Maintaining good hygiene practices is essential to prevent the spread of contaminants and protect your health when working with chemicals. Practicing good hygiene helps minimize the risk of unintentional ingestion or absorption of harmful substances.
Consider the following hygiene practices:
- Hand Washing: Thoroughly wash your hands with soap and water before and after handling chemicals or removing PPE. Follow proper hand washing techniques, including lathering for at least 20 seconds and rinsing with clean water.
- Avoid Touching Face or Mouth: Avoid touching your face, mouth, or eyes when working with chemicals. This reduces the risk of inadvertently transferring chemicals to sensitive areas.
- Clean Personal Protective Equipment (PPE): Regularly clean and decontaminate your PPE according to manufacturer instructions to prevent the accumulation and transfer of chemicals.
- Avoid Eating or Drinking in Chemical Handling Areas: Eating or drinking in areas where chemicals are present increases the risk of ingesting hazardous substances. Designated break areas should be separate from chemical handling areas.
By practicing good hygiene, you can minimize potential exposure to chemicals and maintain a safe and healthy working environment.
7. Fire Safety
7.1 Preventing Fire Hazards
Fire hazards can be present when working with certain chemicals. It is essential to identify and mitigate potential ignition sources and implement preventive measures to minimize the risk of fires.
Consider the following fire prevention tips:
- Proper Handling and Storage: Follow safe handling and storage procedures for flammable chemicals. Ensure that containers are properly sealed and stored in accordance with relevant regulations and guidelines.
- Eliminate Ignition Sources: Regularly inspect your work area to identify potential ignition sources such as open flames, sparks, or hot surfaces. Eliminate or control these sources to reduce the risk of fire.
- Implement Proper Housekeeping Practices: Keep work areas clean and free of flammable materials, such as paper, rags, or other combustible substances. Remove clutter and ensure that access to fire extinguishers and emergency exits is unobstructed.
- Control Static Electricity: Static electricity can ignite flammable vapors or dust particles. Implement measures, such as bonding and grounding, to control static electricity in areas where flammable materials are present.
7.2 Fire Extinguishers and Suppression Systems
Having the appropriate fire extinguishers and suppression systems in place is crucial for promptly extinguishing small fires or controlling larger fires before they spread.
Consider the following guidelines for fire extinguishers and suppression systems:
- Types of Fire Extinguishers: Select fire extinguishers appropriate for the types of fires that may occur in your workplace. Different extinguishers are designed for different types of fires, such as those fueled by flammable liquids, electrical equipment, or combustible materials.
- Proper Placement of Fire Extinguishers: Install fire extinguishers in easily accessible locations throughout your workplace. Place them near exits, in areas where fire hazards are present, and on each floor of the building.
- Maintenance and Inspection: Regularly inspect and maintain fire extinguishers to ensure they are in good working condition. Follow the manufacturer’s recommendations for maintenance and schedule professional inspections as required.
- Suppression Systems: In areas where large quantities of flammable chemicals are present, consider the installation of automatic fire suppression systems, such as sprinklers or foam systems. These systems can quickly control or extinguish fires without relying on manual intervention.
7.3 Emergency Evacuations and Fire Drills
Emergency evacuations and fire drills are essential to ensure that all employees are prepared and know what to do in the event of a fire. Regular practice and preparedness can save lives and minimize injuries.
Consider the following practices for emergency evacuations and fire drills:
- Develop an Evacuation Plan: Create a comprehensive evacuation plan that includes evacuation routes, assembly points, and procedures for verifying that everyone has safely evacuated. Clearly communicate this plan to all employees.
- Conduct Regular Fire Drills: Schedule fire drills at regular intervals to practice the evacuation plan and familiarize employees with emergency procedures. Use the drills to identify any deficiencies or areas for improvement.
- Assign Roles and Responsibilities: Designate specific employees to act as evacuation wardens or fire safety officers who will oversee the drill or emergency evacuation. These individuals should be trained and knowledgeable in fire safety procedures.
- Review and Improve: After each fire drill, conduct a debriefing session to assess the effectiveness of the evacuation plan and identify areas for improvement. Continuously review and update the plan based on best practices and feedback.
By prioritizing fire safety and conducting regular drills, you can ensure that employees are adequately prepared to respond to fires and evacuate safely.
8. Hazardous Waste Management
8.1 Identifying and Labeling Hazardous Waste
Proper identification and labeling of hazardous waste is crucial for ensuring its safe storage, transportation, and disposal. Failure to handle hazardous waste correctly can have serious consequences for the environment and human health.
Consider the following practices for identifying and labeling hazardous waste:
- Conduct a Waste Assessment: Evaluate the waste generated in your workplace to identify hazardous substances. Consider consulting relevant regulations and guidelines to determine what constitutes hazardous waste.
- Segregate Hazardous Waste: Separate hazardous waste from non-hazardous waste to facilitate proper management and disposal. Store hazardous waste in designated containers or areas to prevent cross-contamination.
- Label Hazardous Waste Containers: Clearly label containers of hazardous waste with appropriate hazardous waste labels. Include essential information, such as the contents, hazard classification, and proper handling precautions.
- Review and Update Labels: Regularly review and update hazardous waste labels to ensure accuracy and compliance with local, state, and federal regulations. Remove or properly dispose of any outdated or illegible labels.
8.2 Storage and Disposal of Hazardous Waste
The proper storage and disposal of hazardous waste is crucial for protecting the environment and complying with regulatory requirements. Implementing safe practices when handling hazardous waste is essential to prevent accidental releases or contamination.
Consider the following guidelines for storing and disposing of hazardous waste:
- Proper Storage Containers: Store hazardous waste in appropriate containers that are compatible with the waste being stored. Ensure that containers are kept tightly sealed to prevent leaks or spills.
- Secondary Containment: Use secondary containment measures, such as trays or spill containment systems, to capture and contain any leaks or spills that may occur during storage.
- Secure Storage Areas: Designate specific storage areas for hazardous waste that are secure, well-ventilated, and inaccessible to unauthorized personnel. These areas should be clearly labeled and equipped with appropriate safety equipment, such as fire extinguishers or spill control kits.
- Proper Disposal: Comply with all applicable regulations when disposing of hazardous waste. Identify and work with licensed waste management professionals or facilities to ensure proper disposal practices.
By adhering to proper storage and disposal practices, you can effectively manage hazardous waste and prevent contamination of the environment and potential harm to human health.
8.3 Compliance with Waste Regulations
Compliance with waste regulations is essential in ensuring the safe and legal management of hazardous waste. Various local, state, and federal regulations govern the handling, storage, transport, and disposal of hazardous waste. Familiarize yourself with these regulations and ensure your workplace adheres to them.
Consider the following practices for compliance with waste regulations:
- Stay Informed: Regularly monitor and stay updated on applicable waste regulations. Consult local or national environmental agencies, as well as industry associations or professional organizations for guidance and updates.
- Training and Education: Provide employees who handle or manage hazardous waste with proper training on waste regulatory requirements. Ensure they understand their responsibilities and the consequences of non-compliance.
- Record Keeping: Maintain accurate and up-to-date records relating to hazardous waste management. This includes waste assessments, waste generation and disposal documentation, and any permits or licenses required by regulatory agencies.
- Periodic Audits and Inspections: Conduct internal audits and inspections to assess compliance with waste regulations. Identify any deficiencies, implement corrective actions, and continuously improve waste management practices.
By prioritizing compliance with waste regulations, you can effectively manage hazardous waste and maintain a safe and environmentally responsible workplace.
9. Chemical Spill Response
9.1 Developing a Spill Response Plan
Having a well-prepared spill response plan is crucial for effectively managing and mitigating the impact of chemical spills. A spill response plan establishes the necessary procedures and protocols to ensure a swift and safe response in the event of a spill.
Consider the following when developing a spill response plan:
- Hazard Assessment: Conduct a thorough hazard assessment to identify potential spill hazards and their associated risks. Consider the types and quantities of chemicals used, as well as potential impact on personnel, the environment, and property.
- Spill Response Team: Designate and train a spill response team responsible for effectively managing and coordinating spill containment, cleanup, and communication efforts. Ensure that team members are familiar with the spill response plan and their assigned roles.
- Emergency Contacts: Compile a list of emergency contacts, including internal and external personnel, such as management, environmental agencies, and emergency services. Provide clear instructions on who to contact and when, to facilitate timely response and assistance.
- Communication Procedures: Establish clear communication channels and procedures for reporting spills and initiating the spill response plan. Define how information is to be relayed to appropriate personnel and how updates and notifications will be disseminated.
9.2 Containing and Neutralizing Spills
The immediate containment and neutralization of chemical spills are critical to preventing further damage or harm. A prompt and efficient response can help minimize the spread of the spill and mitigate potential risks.
Consider the following guidelines for containing and neutralizing chemical spills:
- Personal Safety First: Ensure the safety of spill responders by providing appropriate personal protective equipment (PPE). Individuals responding to spills should be properly trained in spill response procedures and equipped with the necessary safety gear.
- Isolate the Spill Area: Establish physical barriers or cordons to isolate the spill area and prevent unauthorized access. Restricting access helps protect personnel and prevents the spread of the spill.
- Use Absorbent Materials: Deploy appropriate absorbent materials, such as spill kits or absorbent pads, to contain and absorb the spilled chemical. Select absorbents that are compatible with the spilled substance, considering potential reactivity or chemical incompatibilities.
- Neutralize as Appropriate: If applicable and safe to do so, neutralize the spilled chemical according to established procedures. Follow manufacturer instructions, if available, or consult experts or local authorities for guidance on neutralization techniques.
By following proper spill containment and neutralization procedures, you can minimize the extent and impact of chemical spills and safeguard personnel and the environment.
9.3 Reporting and Cleanup Procedures
Proper reporting and cleanup procedures ensure that chemical spills are appropriately managed and that steps are taken to mitigate any lingering hazards. Accurate documentation and complete cleanup promote a safe working environment and prevent future issues.
Consider the following practices for reporting and cleanup procedures:
- Report the Spill: Immediately report the spill to the appropriate personnel or authorities, following the established communication procedures. Provide accurate and detailed information about the spill, including its location, the substances involved, and any known hazards.
- Cleanup Planning: Develop a cleanup plan, considering the hazards associated with the spilled substance and any regulatory requirements. Identify the necessary cleanup resources, equipment, and personnel to ensure an effective and efficient cleanup process.
- Waste Disposal: Properly handle and dispose of all waste generated during the spill cleanup process. Segregate waste according to its hazardous nature and dispose of it in accordance with applicable regulations and waste management practices.
- Decontamination: If necessary, decontaminate affected surfaces or equipment to ensure their safe and clean condition. Follow established decontamination procedures and use appropriate cleaning agents and personal protective equipment.
By promptly reporting spills, thoroughly planning cleanup efforts, and properly disposing of waste, you can effectively manage chemical spills and minimize potential hazards.
10. Regular Safety Audits and Inspections
10.1 Conducting Routine Inspections
Routine safety audits and inspections are essential for identifying potential hazards, assessing compliance with safety protocols, and promoting continuous improvement. Regular inspections help ensure that all safety measures are in place and functioning correctly.
Consider the following practices for conducting routine inspections:
- Develop an Inspection Checklist: Establish a checklist to guide inspectors during routine safety audits. Include all relevant safety requirements, procedures, and equipment that need to be assessed.
- Conduct Systematic Inspections: Systematically inspect the workplace, focusing on areas where hazards are likely to occur, such as chemical storage areas or handling stations. Ensure that inspections cover all relevant safety aspects outlined in the inspection checklist.
- Involve Employees: Encourage employees to actively participate in safety inspections by reporting potential hazards or suggesting improvements. Their input can provide valuable insights and enhance safety awareness.
- Document Findings and Recommendations: Document inspection findings, including any non-compliant areas, hazards, or recommended corrective actions. This documentation serves as a reference for addressing safety concerns and tracking progress over time.
10.2 Addressing Safety Concerns
Identifying safety concerns is only the first step; taking prompt action to address them is equally important. Whether it involves repair work, procedural changes, or additional training, addressing safety concerns promptly helps minimize risks and fosters a safer working environment.
Consider the following strategies for addressing safety concerns:
- Implement Corrective Actions: Prioritize and implement corrective actions based on the severity and urgency of identified safety concerns. Develop action plans that outline the steps, responsible parties, and timelines for each corrective action.
- Conduct Training and Education: If safety concerns are related to employee knowledge or skills, provide additional training or education to address the gaps. Ensure that employees are aware of any changes or improvements made to safety protocols.
- Seek Expert Advice: For complex or specialized safety concerns, consult experts or professionals in the field. They can provide guidance, recommendations, or solutions based on their knowledge and experience.
- Regular Follow-Up: Regularly follow up on implemented corrective actions to assess their effectiveness and evaluate any new risks or concerns that may arise. Continuously monitor and improve safety performance based on feedback and lessons learned.
By promptly addressing safety concerns, you demonstrate a commitment to maintaining a safe working environment and protecting the well-being of all employees.
10.3 Continuous Improvement
Continuous improvement is a fundamental principle in ensuring long-term safety and risk reduction. Regularly reviewing and enhancing safety programs, procedures, and controls allows for the identification and implementation of best practices.
Consider the following strategies for continuous improvement:
- Management Commitment: Foster a culture of continuous improvement by involving management and leadership in safety initiatives. Their commitment and support are essential for promoting a proactive safety mindset across the organization.
- Employee Involvement: Encourage employees to actively participate in safety improvement efforts. Solicit their feedback, suggestions, and observations to identify areas for improvement or alternative approaches.
- Regular Safety Meetings: Conduct regular safety meetings or toolbox talks to discuss safety performance, share lessons learned, and identify opportunities for improvement. These meetings provide forums for open communication and promote a collective commitment to safety.
- Benchmarking and Industry Standards: Compare your safety programs and practices to industry benchmarks and standards. This allows you to identify gaps and adopt best practices from other organizations to continuously enhance safety performance.
By embracing a culture of continuous improvement, you can proactively identify and address safety gaps, ultimately creating a safer workplace for everyone.
In conclusion, working with chemicals requires a comprehensive approach to safety. By understanding and adhering to PPE requirements, implementing proper chemical handling and storage practices, conducting risk assessments, being prepared for emergencies, ensuring ventilation and engineering controls are effective, practicing safe work habits, and understanding fire safety, hazardous waste management, chemical spill response, and regular safety audits and inspections, you can significantly reduce the risks associated with working with chemicals. Remember, your safety is paramount, and by following these guidelines and continuously improving your practices, you can create a safer and healthier work environment.